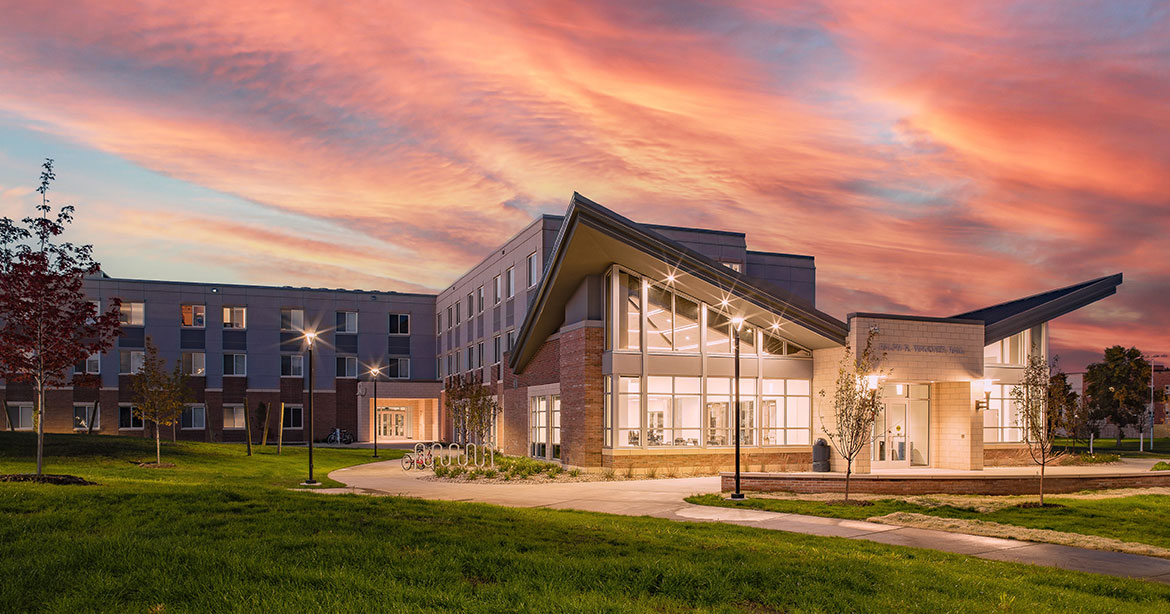
Augustana University, the largest private university in South Dakota, partnered with Mortenson to execute a five-year master plan to address their on-campus student housing shortage. The first phase included a new 54,000-square-foot, three-story residence hall with 208 beds and open-concept community spaces.
The university had a strict schedule with no wiggle room. Construction would commence in the winter, and they needed the new residence hall to be open and ready to welcome students by fall. Additionally, the budget needed to stay within the university’s cost-per-square-foot parameters.
It was 2021, and the construction industry was dealing with supply chain issues and unpredictable material costs that threatened budgets and project schedules. Mortenson and its design partners collaborated to develop a plan to build Augustana University’s South Residence Hall efficiently, and with quality materials, while staying on budget and hitting the critical timeline.
Innovative Custom Prefabrication
The idea of prefabrication was introduced to save time and offer more control over material pricing. The team leveraged Minneapolis-based BLUvera, a Mortenson sister company that manufactures prefabricated panels for commercial construction. The structural engineer evaluated the design and identified different systems the team could use to construct the new residence hall. After reviewing options with the project team, they decided upon a Design for Manufacture and Assembly (DfMA) approach using prefabricated exterior and interior panels.
The difference between DfMA and standard prefabricated construction materials is the ability to optimize the product’s design to meet specific functional and installation criteria. In the case of Augustana, the proposed solution was customized panelized wall interior and exterior systems with precast structural slabs.
“We had a lot of conversations with BLUvera, structural engineers, and the design team to see how this would work,” says Joanna Slominski, market director. “We wanted to save time and be efficient, but also had a lot of structural considerations to consider in addition to how to sequence the installation of everything on site. In the end, we developed a solution that would save time and produce high-quality results.”
40% Schedule Savings Over Traditional Building Methods
Using traditional building methods, constructing the residence hall exterior would require several weeks and multiple steps: setting the steel structure, framing and sealing the exterior walls, installing sheeting and vapor barrier, and then installing and sealing windows. After that, crews would need to lay slabs for each floor, repeating the process until all stories were complete. Each of these steps is typically performed by a separate trade partner, requiring more coordination, and more time to execute.
The BLUvera exterior wall panels included all the components—structural stud framing, sheathing, vapor barrier, and windows—in single panels that created a water-tight structure. All crews needed to do was add the final finishes after installation. As soon as each series of panels went up, crews could follow behind placing the precast hollow core planks.
“This is where the biggest schedule savings happened,” says David Thorson, development senior project manager. "With the exterior wall panels already having sheathing, vapor barrier, and windows in place, we were able to commence interior construction immediately after a floor was completed structurally." Additionally, the panels helped minimize the need to install temporary enclosure measures for temporarily heating the building. Installing all 330 structural panels only took four weeks, shaving 40% off the construction schedule.
Time-Saving Sequenced Installation
While more efficient than a standard exterior construction approach, building a university residence hall with prefabricated panels still requires precise coordination. The schedule didn’t allow any room for delays and the job site had limited storage space.
The solution was a structural sequence drawing detailing the exact number of prefabricated panels and precast slabs needed for each section. BLUvera used this information to manufacture the panels and transport them to the job site, which was five hours away from their manufacturing facility. Each series of panels arrived a few days before the scheduled installation to avoid storage capacity issues and prevent installation delays.
Instead of tackling the structure in multiple stages, the team could lay the foundation, install the panels, and place the precast concrete planks on top of the installed walls to start building the next floor. “It was significantly more efficient than a standard build,” says David. “The prefabricated panels allowed us to sequence installation in a manner to where we could install the walls for a section, then have the precast team follow behind to start setting the floors.”
The traditional method of completing the exterior structure would have taken several months to finish. By introducing DfMA prefabricated panels, Mortenson completed this phase of the project in four months and wrapped up the entire project in time for students to move in.
Applying Knowledge to Future Higher Education Construction Projects
Any new or innovative approach to building takes time to learn and master. There are takeaways from each project that help teams refine processes and continue pushing the envelope of innovation in higher education construction. After seeing the success of Augustana’s South Residence Hall, Mortenson is working with BLUvera to elevate the design of prefabricated structural walls and find ways to use them in other projects.
Your Partner in Higher Education Construction
Bring your visions to life with a team invested in making your campus construction project successful. With a proven track record of excellence, there’s no limit to what we can achieve together.